在螺栓连接中,有一种断裂现象被称为疲劳断裂。这种断裂多发生在振动安装环境中,与氢脆一样属于突发性失效问题。由于现有技术无法提前预知螺栓何时会发生疲劳断裂,因此必须从源头进行预防。
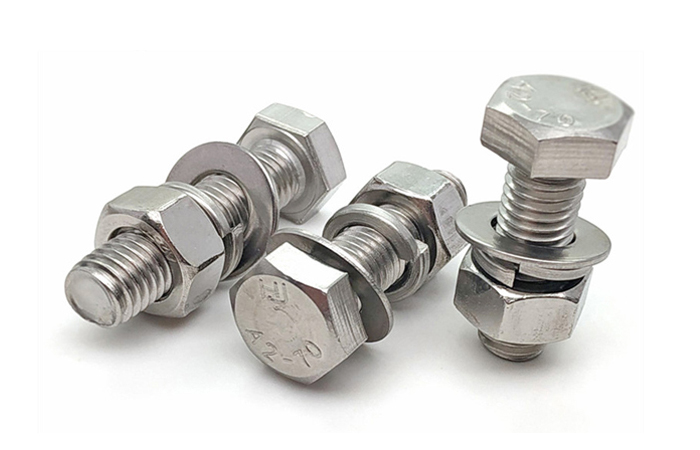
任何螺栓都有使用寿命,虽然螺栓属于可重复使用的产品,但并非可以无限次使用。当螺栓长期处于超强负载环境时,发生疲劳断裂的概率会显著增加。这类断裂不仅会对生产设备造成严重破坏,甚至可能引发安全事故。
关于螺栓疲劳断裂的成因,目前较为统一的观点是:由于螺栓使用环境与配合零件的基础材料存在差异,且安装的可活动零部件形状尺寸各不相同,当螺栓连接过紧时,局部会出现应力集中现象。若应力超出材料承受极限且材料可塑性不足,螺栓会逐渐产生微裂纹。这些微观裂纹在循环应力作用下不断扩展,当达到临界值时,螺栓会突然断裂。虽然肉眼观察到的是瞬间断裂,但实际上裂纹是经过长期累积形成的。其发展过程可概括为:
安装过程中产生应力集中点
应力持续作用导致基体材料逐渐分离
形成宏观可见的微小裂纹
裂纹扩展至临界尺寸引发瞬时断裂
应力集中:螺纹根部、螺栓头部过渡区等部位易形成应力集中
循环载荷:长期交变载荷加速裂纹扩展
环境因素:
材料性能:
优化结构设计:
采用 R 角螺纹设计(减少应力集中)
增加螺栓头部过渡圆角
优先选用半牙螺栓(光杆部分耐疲劳性更强)
工艺改进:
调整加工顺序:先热处理后搓牙
实施表面强化处理(喷丸 / 滚压)
使用规范:
抗拉强度测试:
通过拉断试验评估材料性能
观察断裂位置判断薄弱环节
记录断裂载荷作为参考依据
环境模拟测试: