在机械工程领域,氢脆是高强度螺栓失效的主要隐性风险之一,其危害源于氢原子对金属晶格的侵蚀。本文从科学原理、材料特性、诱发机制及防控措施展开严谨分析,为工程实践提供专业指导。
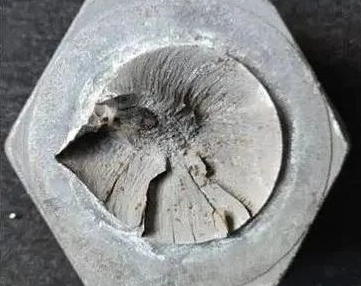
氢脆是指原子态氢渗入金属内部后,在应力作用下向晶界、位错等缺陷处偏聚,形成氢分子并产生内应力,*终导致材料脆性断裂的现象。其核心特征为:
微观机制
:氢原子通过晶格间隙扩散,在夹杂物、晶界等 “氢陷阱” 处结合为氢分子,产生高达 300-500MPa 的内应力,超过金属晶界结合强度;宏观表现
:材料延伸率从正常 12%-15% 骤降至 2%-5%,冲击韧性下降 60%-80%,断裂前无明显塑性变形,呈典型的沿晶断裂形貌。
氢脆敏感性与螺栓的强度等级、热处理组织密切相关,具体如下:
| | | | | | |
---|
| | | | | | |
| | | | | | 极端酸洗条件(时间>30 分钟)下可能发生,概率<3% |
| | | | | | 电镀锌后若不去氢,72 小时内延迟断裂概率达 20%-30% |
| | | | | | 酸洗后氢含量易超标,未去氢时断裂风险超 40%,常见于镀后 24-48 小时 |
化学反应
:
主反应(除锈):FeO + 2HCl → FeCl₂ + H₂O
副反应(析氢):2H⁺ + 2e⁻ → H(原子态氢)关键影响因素
- 酸液浓度:盐酸浓度>15% 时,析氢量增加 40%,建议控制在 10%-12%;
- 酸洗温度:超过 60℃时,氢扩散速率提升 3 倍,理想温度为 40-50℃;
- 酸洗时间:每增加 10 分钟,氢渗透量增加 30%,10.9 级螺栓酸洗时间应≤15 分钟。
改进方案
:采用缓蚀剂酸洗(如添加 3g/L 乌洛托品),可抑制 80% 的析氢副反应,使氢渗透量从 1.2ppm 降至 0.5ppm 以下。
电镀阴极反应
:Zn²⁺ + 2e⁻ → Zn(主反应),2H⁺ + 2e⁻ → H₂↑(副反应,析氢率 10%-15%);氢陷阱形成
:电镀应力导致晶格畸变,为氢原子提供聚集位点,尤其在螺纹根部、头部过渡圆角等应力集中区。
| | |
---|
| | 阴极析氢反应显著,未去氢时 72 小时内延迟断裂风险高 |
| | 高温锌液加速氢逸出,但若冷却过快(>30℃/ 分钟),氢原子重新聚集导致延迟断裂 |
| | 无酸洗工序,氢渗透量<0.5ppm,无需专门去氢处理 |
优选除锈工艺:
- 10.9 级以上螺栓优先采用喷砂除锈(0.8mm 石英砂,0.6MPa 压力),避免酸洗;
- 若必须酸洗,采用 “双槽酸洗”(**槽 10% 盐酸 + 3g/L 缓蚀剂预洗 5 分钟,第二槽 8% 盐酸精洗 10 分钟),总时间≤15 分钟。
表面活化优化:
电镀锌前改用电解活化(电流密度 0.5A/dm²,时间 2 分钟),减少析氢。
工艺参数:
- 入炉时间:电镀 / 涂层后 2 小时内(氢原子未形成稳定陷阱);
- 温度控制:190-200℃(低于螺栓回火温度 20-30℃,避免硬度下降);
- 目标效果:氢含量≤1.0ppm(采用 GB/T 32566 热导法检测)。
设备要求:
使用带有温度均匀性控制的热风循环炉(温差 ±5℃),禁止使用箱式电阻炉。
| | | |
---|
| | ≤1.5ppm(10.9 级)/≤1.0ppm(12.9 级) | |
| | | |
| | | |
| | | |
选用低氢脆材料:
采用含钛、钒的合金钢(如 35CrMoV),形成稳定碳化物减少氢扩散;替代表面处理:
对高风险螺栓(12.9 级)采用机械镀锌或无铬达克罗涂层,避免电镀锌的强析氢过程。
2019 年某石化装置因循环氢压缩机螺栓氢脆断裂,导致氢气泄漏引发爆炸,直接经济损失超 5000 万元。事故调查报告显示:失效螺栓为 12.9 级,未进行去氢处理,氢含量达 3.5ppm,远超标准限值。这一案例表明,对于 10.9 级及以上高强度螺栓,去氢处理是保障工程安全的必需工序,任何成本妥协都可能引发灾难性后果。
通过材料选择、工艺优化与质量检测的多维度管控,可将氢脆风险降至*低,确保关键连接部位的长期可靠运行。